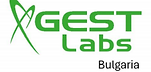


The Gestlabs laboratory offers the Failure Analysis service on printed boards, components and finished products.
It uses the X-Ray analysis, C-SAAM and metallographic microsections for the component’s constructive analysis like MLCC, resistances and active components; datasheet electrical test for the characterisation of passive components like resistances, capacities, inductances, wirings and of the discrete active components like diodes, Mosfet, IGBT, Transistors. It is also able to perform the Decapsulation for the superficial analysis of dies and wire bonding.
For the Failure Analysis of PCB and PCBA, the Gestlabs lab can make the dimensional checks of conductors and of superficial insulations of printed boards; it can check the metallization and the stack-up through metallographic microsections and/or make the SEM-EDX electron microscopy analysis. Furthermore, it can check the compliance with IPC standards through X-Ray analysis and optical analysis.
Among the analytic techniques used in the failure analysis process, the Gestlab laboratory can use techniques like FT-IR (Fourier Transform InfraRed Spectroscopy) analysis for the organic compounds research, the electrical checks (voltage, continuity), the Dye & Pry, and the SEM-EDX electron microscopy analysis.
In the defectiveness analysis of the product, we can define the Failure Analysis path, to perform the analysis of stress condition of components due to the design, and to measure and perform the electrical characterisation at full capacity and during the transients.
We can perform the Failure Analysis of active and passive components, to make the infra-red heat map with measurements on components in the thermal camera, to simulate the failures, and to define the possible solutions.
FAILURE ANALYSIS SERVICES
Some Failure Analysis services offered by our lab include:
-
Circuit analysis of product
-
Electrical characterisation
-
Tomography (3D): check and research of defectiveness, dimensional analysis, evaluation of voids volume, reverse engineering with methods approved by AIPnD (the Italian association of Non-Destructive testing and Diagnostic Monitoring)
-
Scanning Acoustic Microscope (C-SAM): ultrasounds for defining the delaminations/voids of integrated components and other materials.
-
Decapsulation of electrical discrete components and MSI (medium Scale integrate) through chemical etching
-
Analysis through electron microscopy and microsections
FAILURE ANALYSIS PROCESS
The Failure Analysis is a critical process to determine how and why a product, or a component is not able to work in a correct way. The aim is to minimise or remove the risk of event repetition which caused the failure.
METROLOGY AND DIMENSIONAL ANALYSIS
The lab uses advanced instruments of measure
Gestlabs lab has a dedicated area for the dimensional analysis in a controlled temperature and humidity environment, and it uses advanced measurement equipment.
The offered service includes a report certifying the compliance of the product with the constructive design, and the measurements are performed with high-definition optical scan machines and with benchtop instruments.

Computerized Measuring Machine per misure assi X,Y,Z lineari
Non-contact measurements
OGP Smartscope FLASH 400 optical measuring machine non-contact dimensional measurements with a 3-D coordinate measuring machine with OGP Smartcode camera (high definition of 0,003 mm).
BGA Balls coplanarity, balls height
Field of use: 450x450x200 mm
Margin of error:
XY =+/- (3.0 + 8L/1000) micron
Z =+/- (4.0 + 8L/1000) micron
MEASUREMENT OF BOW&TWIST ON PCB
BOW: Deviation of planarity of a sheet, characterised by an approximately spherical or cylindrical curvature so that if the product is rectangular, its four corners are at the same level.
TWIST: Deformation of a panel or a rectangular sheet which occurs on its surface in parallel at one of the diagonal lines so that one of the corner is not at the same level of the other three ones.
Test method: IPC TM 650 2.4.22C (bow and twist percentage of individual rigid printed boards, rigid portions of rigid-flex printed boards, and/or multiple printed panels)


XRF (X-Ray Fluorescence) FOR THE MEASUREMENT OF FINISHING THICKNESSES
The XRF spectrophotometry is a non-destructive analysis technique which allows to evaluate the thickness of the sheets finishing thanks to the analysis of the x-rays released by it (the so-called x-ray fluorescence) after the atomic excitation with the suitable power.
AVAILABLE INSTRUMENTS
-
Measuring microscope (field 100 x 100 mm)
-
Measuring microscope (field 50 x 50 x 10 mm)
-
Torque wrench up to 35 N m
-
2 load cells for torque (up to 10 N m)
-
2 torque screwdrivers (up to 8 N m)
-
Comparators
-
Micrometres
-
Analogical and digital gauges
-
Samples for metric and American threads
-
Precision balance up to 1000 g
METALLOGRAPHIC
ANALYSIS
The science able to observe the inner structure of a material
The metallographic analysis is needed to understand the chemical, physical, mechanical, and technological features of metal materials, to evaluate the working conditions influence on the behaviour of the materials, to check the reaction of a material to the specific requests, and to identify possible anomalies and the relative causes.
The metallography is a science which observes the inner structure of a material by studying the crystal morphology. The details obtained by the metallographic analysis allow to check the condition of the material.

MAIN PERFORMED TESTS
The metallographic tests.
-
Metallographic microsections
Metallographic microsections
The cross section metallographic analysis is a destructive analysis which allows to check the right construction of the printed board by verifying the copper thickness in the inner layers and on the surface, the right application of solder mask, the metallisation of the inner holes, and the quality of the circuit boring.
The sample is sectioned and integrated into a specific resin; then by further mechanical processing, and the lapping of the to-be-analysed surface, it is observed through the optical microscopy.
Test method: IPC TM 650 2.1.1 (Micro sectioning, Manual method)
-
Analysis with optical microscope
The optical microscopy is a method of investigation essential for the structure analysis of the materials. This technique is effective for the study of the anomalies due to thermal treatment, for the evaluation of the inclusions, for identifying the breaks, and for the evaluation of the soldering and the coatings.
Technical regulations: IPC A-600 (Acceptability of Printed Boards), IPC A-610 (Acceptability of Electronic Assemblies), IPC 6012 (Qualification and Performance Specification for Rigid Printed Boards)
-
SEM (Scanning Electron Microscope) – EDX (Energy Dispersive X-Ray) Spectroscopy
The Scanning Electronic Microscope indicated as SEM is a type of microscope which allows a morphological investigation at high magnifications.
With the word EDX (Energy Dispersive X-ray Analysis) Spectrophotometry we indicate an instrumental analytical method whose work is based on the interaction between a primary focused electron beam which beats the sample and the electrons of the atom that constitute the sample itself.
The combined use of the two techniques allows the morphological characterisation (SEM) and the compositional one (EDX), and it provides with an instrument for the understanding of the composition of material structure.
-
Dye&Pry Test
The Dye&Pry analysis technique is a destructive test used when it is impossible to solve a problem with the optical inspection (for example in case of too small defects).
This technique is based on the use of a liquid colourant which soaks into the microfractures existing on the soldering. When the colourant is dried, the electronic components (BGA, condensers, resistances, etc.) are removed from PCB and the soldering are inspected: the presence of the colourant reveals the problematic areas at the level of connections of all the interfaces.
Test method: Internal Method
-
Solderability Test
The Soldering Test on printed boards is performed on the base of IPC J-STD-003 Standard which describes the procedures and the methods to define the acceptability criteria of the wettability of the superficial finishing of the sheets.
Through this method it is possible to evaluate the weldability of:
-
Superficial conductors;
-
Fixing points;
-
Plated-through holes (PTHs) of printed boards.
The Soldering Test of components is performed on the base of IPC J-STD-002 Standard which sets the testing methods, defines the defects and the acceptability criteria for the evaluation of the weldability of terminals and flexible cables. This test is necessary to check if the weldability of components terminals (lead) follows the requirements requested by the standard.
Test method: IPC J-STD-002 (Solderability Tests for Component Leads, Terminations, Lugs, Terminals, and Wires), IPC J-STD-003 (Solderability Test for Printed Boards)
-
X-Ray (2-D and 3-D defects analysis)
The X-Ray analysis of electronic sheets is a non-destructive technique which allows to identify and evaluate possible failures and/or defects at the level of open, voids, solder ball, and soldering breakouts. Furthermore, this test allows to check the correct soldering of components and to identify possible soldering voids.
The X-Ray analysis allows to find factors which could not be noticed with a simple visual inspection. The evaluation can be performed both through 2-D oriented presentations and 3-D volumetric views.
Technical regulations: IPC A-610 (Acceptability of Electronic Assemblies), IPC 7095 (Design and Assembly Process Implementation for BGAs).
-
Solder Float Test
This test is performed on PTH (Plated-Through-Holes) with the aim of determining if the PTH can support the thermodynamic effects of the extreme heat to which they can be exposed during the assembling, re-working, or restoration phases.
Test method: IPC TM-650 2.6.8 (Thermal Stress, Plated-Through Holes)
-
Peel Strenght Test
The Peel Strength Test is generally used to measure the peel strength of a material, usually of an adhesive.
Through this test is possible to determine the comparative peeling features or breakout force of adhesive bonds tested on samples of specific sizes and in defined conditions of pre-treatment, temperature, and speed of the testing machine.
Test method: IPC TM 650 2.4.8C (Peel Strength of Metallic Clad Laminates)
CHEMISTRY AND SURFACE ANALYSIS
The activities of the chemical lab
The activities of the chemical lab are focused on the quality and quantity analysis of chemical substances to check the compliance with current regulations or the requirements of the examined materials.
As for example the Fourier Transform Infra-Red Spectroscopy (FT-IR) provides with structural information on the analysed material through the interaction between an infra-red radiation and the material itself. This test is suitable to define the quality and the semi-quantity of the organic compounds.
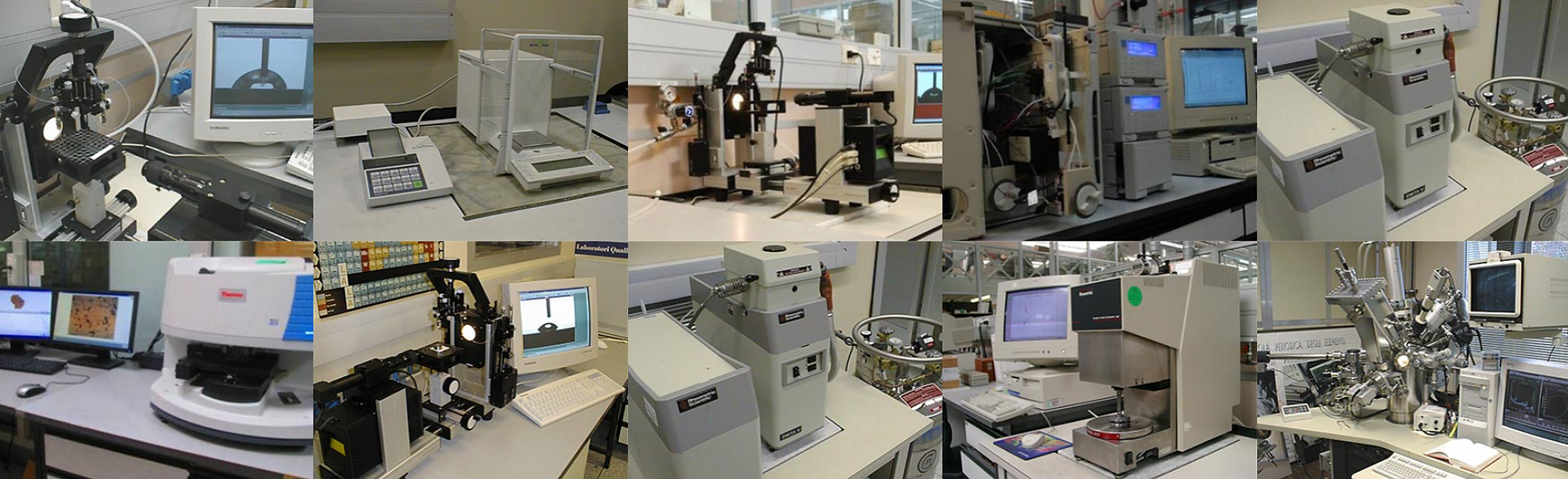
MAIN PERFORMED TESTS
The metallographic tests.
-
FT-IR (Fourier Transform Infra-Red Spectroscopy)
The Fourier Transform Infra-Red Spectroscopy (FT-IR) provides structural information about the analysed material thanks to the interaction of an infra-red x-ray with the material. This test is suitable for the quality and quantity analysis of organic compounds. The FT-IR analysis allows to identify the functional groups inside the molecules and the characterisation is performed comparing the spectra of the databases or by attributing every resulting peak to the vibration of a specific functional group. A limit of the instrument is represented by the fact that in case of analysis of natural organic substances, it allows only the distinction of the compound classes but not the one of the single substances (for example it identifies if a substance belongs to the oil category, but it doesn’t allow to identify which specific substance is).
Test method: ASTM E1252 (Standard Practice for General Techniques for Obtaining Infrared Spectra for Qualitative Analysis)
-
TIC – Total Ionic Contamination
The Ionic Cleanliness test is used to measure the conductivity/resistivity of a solution obtained by the sample treatment. The performed measurement can be related to the quantities of the ionic material on it; the resistivity of the solution decreases when the ionic contamination level increases. Usually, the ionic contaminators are flux residues or harmful materials which derive from the productive process, and they can downgrade the reliability of the electronic components and the assemblies because they contribute to the leaked current among the circuits by easing the dendritic growth and by increasing the corrosion risk.
Test method: IPC TM 650 2.3.25.1 (Ionic Cleanliness Testing of Bare PCBs) – This test is used to determine the total extractable ionic content from printed circuits (PCBs) to control the process.
Test method: IPC TM 650 2.3.25D (Detection and Measurement of Ionizable Surface Contaminants by Resistivity of Solvent Extract (ROSE)) – This test is used as process control instrument, and it can be used both in printed circuits and assemblies.
-
Inductively Coupled Plasma – Optical Emission Spectrometry
The Optical Emission Spectrometry (OES) is an analytical technique which allows to identify the traces of metal and uses the Inductively Coupled Plasma (ICP) to separate the sample into atoms and ions, that opportunely excited, release an electromagnetic radiation of different wavelength according to each element.
This test allows to determine the basic quality and quantity composition of the analysed sample.
Our chemical lab is also able to determine the carbon and sulphur concentration into metal alloys through a carbon and sulphur analyser (LECO). The application field of this analysis includes metals like steel, iron, copper, alloys, etc.
-
Determining the Contact Angle
The contact angle is a thermodynamic quantity which represents a measurement of wettability. This test measures the angle a drop of a liquid creates on the surface of a solid. The size of the contact angle between the liquid and the solid depends on the interaction between the substances and the contact surface. Lesser the interaction, greater the contact angle and it will be more difficult to wet the solid, which will have a lesser adhesion to foreign bodies. From the contact angle determination, it is possible to define some features of the surface like, for example, the surface energy.
Test method: ASTM D7490 Standard Test Method for Measurement of the Surface Tension of Solid Coatings, Substrates and Pigments using Contact Angle Measurements
Test method: ASTM D7334 Standard Practice for Surface Wettability of Coatings, Substrates and Pigments by Advancing Contact Angle Measurement
-
Coefficient of Thermal Expansion (CTE) with TMA
The Coefficient of Thermal Expansion describes how the size of an object can change in relation to a temperature variation. Usually, the substances expand themselves when their temperature changes and the relative expansion or reduction can occur in all the directions (isotropic material)
Test method: IPC TM650 2.4.24 (Glass Transition Temperature and Z-Axis Thermal Expansion by TMA)
-
Time to Delamination (with TMA)
The Time to Delamination is a measurement used to evaluate the basic material performance: it provides with an information about the time the resin and the copper require to separate or delaminate themselves. This test uses the TMS instrument to bring a sample (laminated or a printed circuit) at a specific temperature, and it measures the necessary time for the delamination.
Test method: IPC TM 650 2.4.24.1 (Time to Delamination (TMA Method))
-
IC – Ion Chromatography
The Ion Chromatography (IC) is an analytical technique which divides ions and polar molecules depending on their charge. Every species interacts in a different way with the stationary phase (a column full of resin), and they have different retention times. This feature allows to quantify them individually after being separated. The test procedure is designed to measure the ionic contamination level extractable from the surface of printed circuits and assemblies, soldering fluxes, electrical components, etc.
Test method: IPC TM 650 2.3.28 (Ionic Analysis of Circuit Boards, Ion Chromatography Method), IPC TM 650 2.3.28.1 (Halide Content of Soldering Fluxes and Pastes), IPC TM 650 2.3.28.2 (Bare Printed Board Cleanliness by Ion Chromatography)
-
Thermogravimetric Analysis with TGA
The Thermogravimetric Analysis measures the variation of the sample mass subjected to a heating with a controlled growth of the temperature. The result of the analysis includes a thermogram which indicates temperature/time on the x-axis and the absolute change or sample mass percentage on the ordinates (Thermal Decomposition Curve). This analytical technique is useful to evaluate the decomposition and oxidation processes.
Test method: IPC TM 650 2.4.24.6 (Decomposition Temperature (Td) of Laminate Material Using TGA)
-
Solder Pastes Analysis
The solder pastes are suspensions of stable and homogeneous particles of the soldering powder immersed into a liquid flux. By changing the size, the distribution, and the shape of the soldering particles, it is possible to control the rheology and the performances of the pastes.
-
Solder Ball Test – This test is performed to determine the solder paste re-flow properties during the re-fusion process.
-
Ref. Standard IPC TM 650 2.4.43 (Solder Paste – Solder Ball Test)
-
-
Slump Test – This test defines the vertical and horizontal slump of the solder pastes.
-
Ref. Standard IPC TM 650 2.4.35 (Solder Paste – Slump Test
-
-
Wetting Test – The wetting test defines the ability of a solder paste to wet an oxidised copper surface and allows to examine, from the quality point of view, the spatter quantity of the solder paste during the re-fusion process.
-
Ref. Standard IPC TM 650 2.4.45 (Solder Paste – Wetting Test)
-
-
Glass Transition Temperature (Tg)
The Glass Transition Temperature is usually indicated with the symbol Tg, and it represents the temperature range at which an amorphous material moves from a hard, glassy condition to a more flexible, rubbery condition. This phenomenon is the so-called structural relaxation.
It is possible to define the Glass Transition Temperature by using different instruments:
-
TM 2.4.24C Glass Transition Temperature and Z-Axis Thermal Expansion by TMA
-
TM 2.4.25C Glass Transition Temperature and Cure Factor by DSC
-
TM 2.4.24.2 Glass Transition Temperature of Organic Films – DMA Method
-
Determining Water Absorption
The water absorption test is performed to determine the quantity of absorbed liquid in specific environmental conditions. This analysis is affected by factors like the type of material, the additives used, the temperature and duration of the test. The results show the possible performances of the materials into water or in humid environments.
Test method: IPC TM 650 2.6.2.1 (Water Absorption, Metal Clad Plastic Laminates) – Determining of the absorbed water quantity by plastic laminates immersed into distilled water for 24 hours.
-
Copper mirror test
This test allows to detect the active substances inside the fluxes. The solder paste or the flux are placed on a substrate covered with a light copper layer. The presence (or not) of active substances will cause the removal of the copper layer on the substrate by allowing to understand the corrosive behaviour of the flux.
Test method: IPC TM 650 2.3.32 (Flux Induced Corrosion (Copper Mirror Method)), IPC J-STD-004 (Requirements for Soldering Fluxes)
-
Melting Point with DSC
The Differential Scanning Calorimetry (DSC) is a method that, considering the temperature, measures the difference between the thermal fluxes in a sample substance and into a reference, both subjected to a controlled temperature variation. This technique provides with information about the quantity of energy absorbed or released by the sample when it is warmed or cooled.
The common Melting Point of a material is identified with the temperature at which it changes its condition from solid to liquid. During this process, all the energy added to a substance is consumed as heat of fusion and the temperature remains constant. The analysis of Melting Point allows to obtain a first impression about the purity of a substance because some impurities change the fusion range.
-
Flammability Test
The flammability is the capacity of a material to burn or explode by causing fires or combustion. The level of difficulty necessary to provoke the combustion of a substance is determined by the flammability test.
Ref. Standard: UL94 (The Standard for Flammability of Plastic Materials for Parts in Devices and Appliances) – Applicable to plastic material, it can determine the materials’ ability to propagate or put out a flame after having lighted it.
-
Porosity Test
GEST Labs can test samples and materials to evaluate their porosity features and to characterise the empty spaces inside of them.
Test method: IPC TM 650 2.3.24 (Porosity of Gold Plating), Standard IPC 4552 (Specification for Electroless Nickel/Immersion Gold (ENIG) Plating for Printed Circuit Boards)
-
Corrosion Test
The corrosion tests are essential to understand how the materials behave in severe or ongoing use conditions, and they can guarantee the achievement of the complete life cycle. This test eases the prediction, the planning, and the mitigation of the negative effects the corrosion can have on the materials on which they can be used.